Understanding the Fundamentals and Applications of Plastic Extrusion in Modern Manufacturing
In the realm of modern production, the method of plastic extrusion plays an instrumental function - plastic extrusion. This complex process, entailing the melting and shaping of plastic via specialized dies, is leveraged throughout different markets for the creation of varied products. From auto parts to customer goods packaging, the applications are substantial, and the potential for sustainability is just as impressive. Untangling the basics of this process exposes the true convenience and capacity of plastic extrusion.
The Basics of Plastic Extrusion Refine
While it may show up complicated, the principles of the plastic extrusion procedure are based on relatively simple principles. It is a manufacturing procedure wherein plastic is melted and after that formed into a constant profile with a die. The plastic extrusion process is thoroughly used in different markets due to its adaptability, cost-effectiveness, and performance.
Various Sorts Of Plastic Extrusion Methods
Structure upon the standard understanding of the plastic extrusion process, it is required to discover the numerous methods entailed in this manufacturing technique. In comparison, sheet extrusion produces big, flat sheets of plastic, which are normally further processed into products such as food product packaging, shower curtains, and car components. Comprehending these methods is key to using plastic extrusion successfully in modern production.

The Duty of Plastic Extrusion in the Automotive Market
A frustrating bulk of components in modern-day vehicles are products of the plastic extrusion process. Plastic extrusion is largely used in the production of different automobile elements such as bumpers, grills, click for source door panels, and dashboard trim. Therefore, plastic extrusion plays a crucial role in vehicle production.
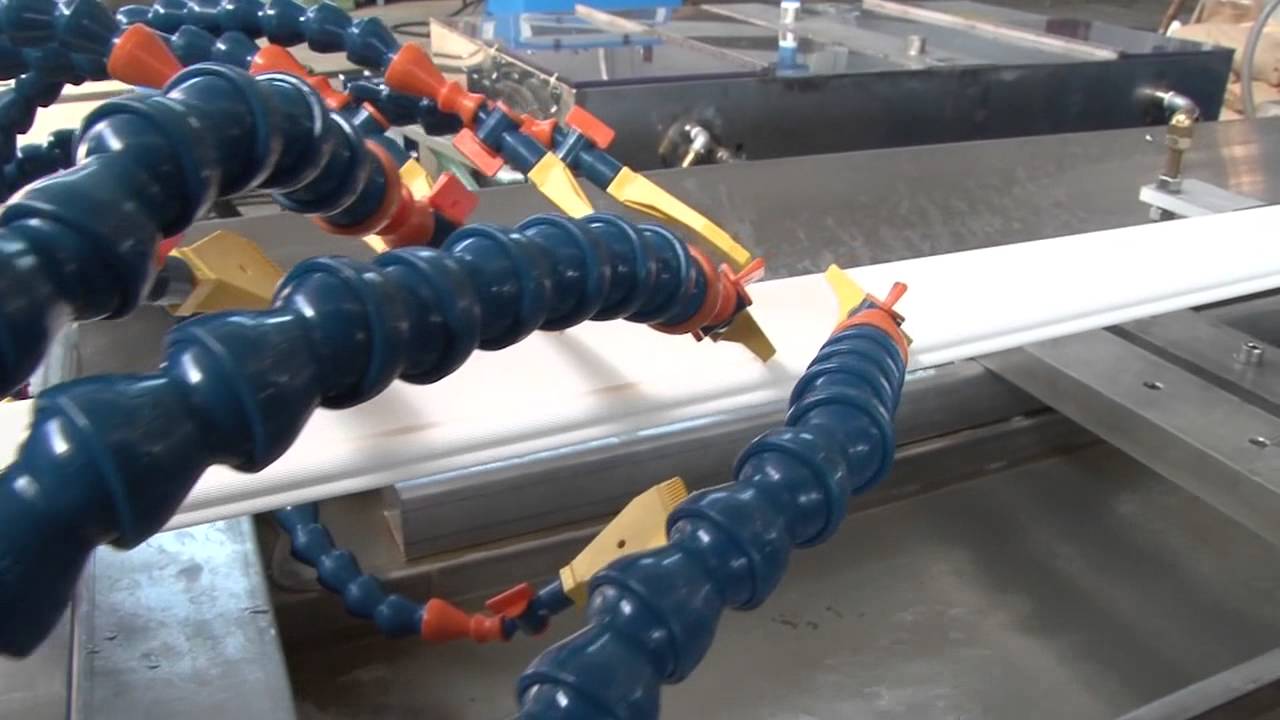
Applications of Plastic Extrusion in Durable Goods Manufacturing
Beyond its substantial effect on the automotive market, redirected here plastic extrusion confirms equally reliable in the world of customer products manufacturing. The convenience of plastic extrusion permits producers to create and generate complicated shapes and dimensions with high precision and performance. The versatility, flexibility, and cost-effectiveness of plastic extrusion make it a preferred choice for lots of customer goods manufacturers, adding considerably to the market's development and technology.
Environmental Effect and Sustainability in Plastic Extrusion
The prevalent use plastic extrusion in manufacturing invites examination of its ecological implications. As a process that frequently uses non-biodegradable products, the ecological impact can be considerable. Power intake, waste manufacturing, and carbon exhausts are all concerns. Nevertheless, industry developments are raising sustainability. Effective equipment minimizes power use, while waste administration systems recycle scrap plastic, decreasing resources needs. In addition, the growth of eco-friendly plastics offers a more environmentally pleasant choice. In spite of these enhancements, better development is needed to mitigate the ecological impact of plastic extrusion. As society leans towards sustainability, producers must adapt to continue to be sensible, emphasizing the relevance of continuous research and innovation in this field.
Final thought
In verdict, plastic extrusion plays an important duty in modern-day manufacturing, especially in the vehicle and consumer items fields. Understanding the essentials of this procedure is vital to optimizing its applications and benefits.

The plastic extrusion procedure is extensively used in different industries due to its cost-effectiveness, versatility, and efficiency.
Structure upon the fundamental understanding of the plastic extrusion procedure, it is Discover More needed to explore the various techniques entailed in this manufacturing method. plastic extrusion. In comparison, sheet extrusion produces huge, flat sheets of plastic, which are usually additional processed into items such as food packaging, shower curtains, and automobile parts.An overwhelming bulk of parts in modern lorries are products of the plastic extrusion procedure